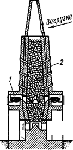
Отечественные автоматические шахтные печи для производства цемента имеют следующие размеры: конструкции СССМ . 2,5 х 10 м; конструкции УЗТМ . 2,55 х 11 м и другие.
Основными элементами печи для изготовления цемента является шахта, загрузочное и разгрузочное устройства, затвор.
Диаметр шахты печи 2,5 м, а высота — 9 м. шахта имеет внешний цилиндрический корпус, изготовленный из стальных листов, и внутреннюю футеровку. Часть шахты на расстоянии 1,2-2 м от верхнего обреза печи выполнена расширяющейся кверху до 2,9-3 м. Некоторое сужение зоны спекания вызвано усадкой материала. Первые три метра шахты футеруются высокоглиноземистым кирпичом, содержащим 65-70% Al2O3. на этих кирпичах не образуются привары; кроме того, они характеризуются большой стойкостью при влажных гранулах. Футеруют зоны подготовки и обжига также магнезитовым огнеупором, титаносодержащим огнеупором и шамотом. Магнезитовый кирпич хорошо сохраняется в случае сухих гранул, поэтому им целесообразно футеровать и зону охлаждения печей. Нижняя часть шахты футерована шамотом класса А. Толщина футеровки в различных печах изменяется от 200 до 350 мм. Стойкость футеровки составляет 6-24 месяца.
К верхней части печи примыкает металлическая труба для отвода дымовых газов, а сама шахта закрыта металлическим колпаком. Подача воздуха осуществляется под колосниковую решетку и через фурмы в зону горения. Предусмотрена подача кислорода в зону горения через верхний конец печи.
Внизу печи размещена колосниковая решетка ступенчатого типа, используемая для выгрузки клинкера. Решетка жестко посажена на вал и приводится от него во вращение. Скорость вращения решетки регулируется в пределах 0,4-1,0 об/ч. Ступенчатая конструкция решетки позволяет изменить высоту столба материала в центре шахты и по ее периферии, что позволяет более равномерно распределять воздух, подаваемый под решетку по сечению шахты.
Загрузочное устройство печи выполнено в виде вращающегося желоба, угол наклона которого регулируется. Над печью расположено устройство для смешения угля с сырьевой смесью и приготовления гранул. Уголь из бункера через весовой дозатор направляется в шнек, в который одновременно поступает сырьевая смесь. Из шнека-смесителя топливно-сырьевая смесь поступает в тарельчатый гранулятор, а затем по желобу-питателю — в печь.
Выгрузка клинкера из печи осуществляется через разгружатель шлюзового типа. Разгружатели изготавливаются двух- и трехшлюзовыми. Клапаны шлюзов попеременно автоматически открываются (в каждый данный момент один клапан открыт, а два других или один закрыты). Таким путем предотвращается выдувание сжатого воздуха из шахты печи. Пройдя последовательно все шлюзы, клинкер поступает на транспортер.
Как уже указывалось, конструкции шахт печи, загрузочных и разгрузочных устройств в настоящее время весьма разнообразны и многочисленны. В частности, имеются печи, загрузочная часть которых выполнена в виде пресс-бегунов или вращающейся тарелки. Катки пресс-бегунов перемещается по днищу, имеющему сужающиеся книзу конические отверстия диаметром 15-30 мм. Сырьевая смесь продавливается через отверстия и в виде цилиндриков длиной 30-100 мм, отрывающихся под действием собственного веса, попадает непосредственно в печь.
При установлении в загрузочной части печи вращающейся тарелки в печь подается уже предварительно брикетированное сырье, брикетики сбрасываются с вращающейся со скоростью 10 об/мин тарелки в печь при помощи специального ножа.
Из цементно-разгрузочных устройств, помимо ступенчатой решетки, следует назвать также круглую колосниковую решетку, вращающуюся на вертикальном валу и покрытую с поверхности зубьями; зубчатую колосниковую решетку, состоящую из двух частей, совершающих возвратно-поступательное движение, разгрузочные зубчатые вальцы